新型氟塑料襯里蝶閥設計、制造與工藝
1、前言
在人類進入“低碳”發(fā)展時代,用最“低碳”設計思維,用最合理的制造工藝,用最經(jīng)濟的材料,實現(xiàn)產品最優(yōu)化,效益最大化,滿足工業(yè)發(fā)展的不同需求,是每個制造商應盡的責任。
隨著現(xiàn)代石油化工工業(yè)的快速發(fā)展,早先年出現(xiàn)的襯橡膠、搪瓷閥門已不能滿足日新月異的工業(yè)需要。人們在不斷的尋求最經(jīng)濟、最合理最低碳的方法來解決這些工業(yè)需要,因此出現(xiàn)了各種材料的襯里閥門,其中氟塑料襯里閥門是襯里閥門中的一朵奇葩。
本文介紹了一種新型氟塑料襯里蝶閥的設計制造與工藝。
2、氟塑料襯里蝶閥的結構與設計
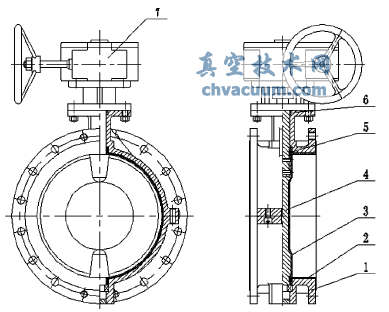
1.閥體 2.閥座襯里層 3.蝶板襯里層 4.蝶板 5.O型密封圈 6.防塵密封圈 7.驅動裝置
圖1 雙法蘭式連接蝶閥
2.1、結構及主要零件名稱
氟塑料襯里喋閥的結構及主要零件名稱如圖1和圖2所示。
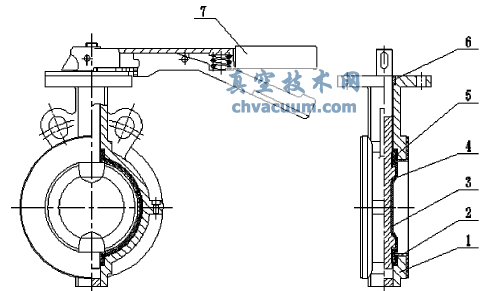
1.閥體 2.閥座襯里層 3.蝶板襯里層 4.蝶板 5.O型密封圈 6.防塵密封圈 7.手柄
圖2 對夾式連接蝶閥
2.2、適用范圍
公稱壓力確定為≤PN16。氟塑料的承受壓力最高可達到2.5MPa,選公稱壓力PN16為保險值。公稱尺寸選定DN50~1200。襯里蝶閥最小公稱尺寸為DN50,最大公稱尺寸DN1200,也有做到1200以上的。
適用溫度:按所選用的不同材料(金屬材料和非金屬材料)能承受的溫度綜合評定。如鋼制襯氟塑料(WCB+F46)材料,使用溫度為-29℃~150℃。限定最高值不超過150℃。
適用介質:低黏度酸、堿類腐蝕性介質。主要指酸性、堿性、有機和無機溶劑等強腐蝕性介質。低黏度是相對濃度較高的顆粒狀介質而言,氟塑料襯里閥門應盡量避免使用固體顆粒的介質。
2.3、結構長度與法蘭尺寸
氟塑料襯里蝶閥結構長度和法蘭尺寸,按鋼制閥門的相關標準和行業(yè)標準執(zhí)行。結構長度按GB/T12221-2005標準中表10的規(guī)定,不論是雙法蘭連接的結構長度還是對夾連接結構長度,均優(yōu)先按短系列選用。如用戶有要求,按合同協(xié)議選用其他結構長度。結構長度包括法蘭密封面襯氟塑料厚度。法蘭連接尺寸一般按GB/T9113.1的規(guī)定。如用戶有要求,可按其他的法蘭標準設計制造。并限制在法蘭端和卡箍連接,不允許采用焊接端連接。因為焊接連接會損壞襯里層而影響產品質量。
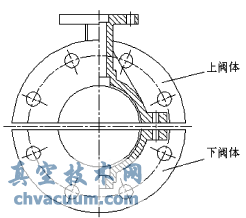
圖3 閥體的上下結構
2.4、閥體設計
2.4.1、閥體結構
閥體的結構為中線密封式,為了適合氟塑料襯里蝶閥的工藝要求,可將閥體設計分為上下兩部分,如圖3,采用沉頭螺栓將上下閥體聯(lián)接在一起。
2.4.2、殼體壁厚與襯里層厚度的確定
氟塑料襯里蝶閥鋼制殼體的最小壁厚依照GB/T12224-2005標準中最小壁厚的給定值作適當加厚,也可參照表1給出的壁厚選取,但必須保證殼體在壓力試驗及模壓工藝條件下不發(fā)生任何有害變形。表1所采用的殼體壁厚,適合于碳素鋼和不銹鋼,也適合球墨鑄鐵,按照這個壁厚設計制造的氟塑料襯里蝶閥經(jīng)過多年的使用,安全可靠。金屬殼體壁厚不包含氟塑料的厚度。氟塑料襯里層厚度的確定既是一個科學問題,又是比較現(xiàn)實的經(jīng)濟問題。應慎重對待,經(jīng)過試驗驗證,確定襯里層厚度δ≥2mm比較合適。并且隨著閥門公稱尺寸的增大而增加。設計時襯里層厚度按相關標準規(guī)定執(zhí)行。也可參照表2的厚度選取。
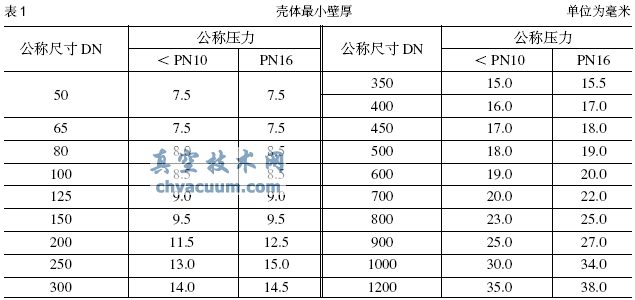
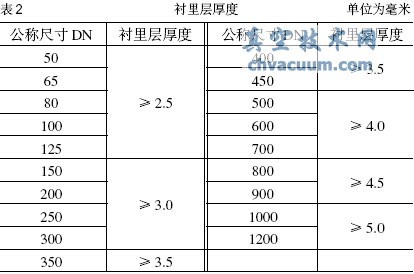
2.4.3、閥體與閥座流道尺寸
閥體密封圈(閥座)與閥體的連接應保證閥門在使用過程中不會松動、不發(fā)生泄漏,對于短結構的閥體法蘭連接(或對夾式連接)的蝶閥,允許有帶螺紋的螺栓孔。閥座流道最小尺寸見表3。
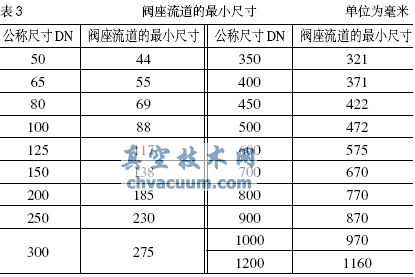
2.5、蝶板與閥軸的設計
2.5.1、蝶板的形狀設計
氟塑料襯里蝶閥的蝶板設計,在強度允許的前提下,應盡量輕薄,呈流線型,如蝶板形狀設計為鐵餅形,蝶板迎水面和出水面設計成流線型,為了不減小蝶板的強度,可增加一些沿流體流動方向的加強筋。從理論上說,蝶板強度應保證在1.5倍最大允許工作壓差下,不發(fā)生變形和損壞。
2.5.2、蝶板的厚度與計算
(1)蝶板厚度(圖4)的設計公式:
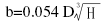
式中:b—蝶板最大直徑,mm;D—蝶閥流道直徑(一般b/D=0.15~0.25),mm;H—最大靜壓水頭(水擊升壓介質),m
H=100(P+△p)
P—設計壓力(常取p=PN),MPa

式中
△p—蝶閥快速關閉時,在管路中產生的水擊升壓值,MPa
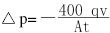
式中:qv—體積流量(查表),m/h;A—閥座通道截面積,mm2;t—蝶板從開全到全關所經(jīng)歷的時間(查表選擇),s
(2)蝶板強度
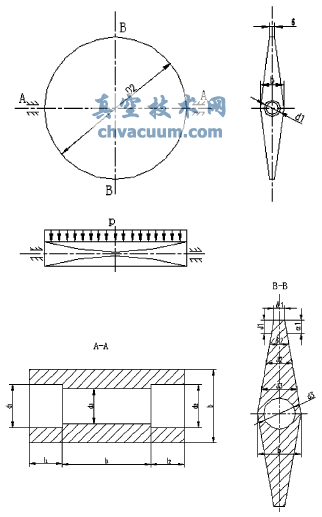
圖4 蝶板尺寸與受力分析
如圖4所示,應對蝶板的A-A斷面積和B-B斷面進行強度校核。
、貯-A斷面的強度效核,A-A斷面的彎應力按式校核:
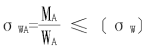
式中:σWA—A-A斷面的彎應力(MPa);MA—A-A斷面的彎矩,(N•mm);WA—A-A斷面的抗彎斷面系數(shù)(mm3)
MA按下式計算:

式中:p—介質中壓力(MPa),設計時可取p=PN。
WA按下式計算:

式中:JA—A-A斷面的慣性矩(mm4)
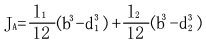
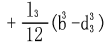
、贐-B斷面的強度效核,B-B斷面的彎應力按下式校核:
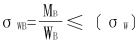
式中
σWB—B-B斷面的彎應力(MPa);MB—B-B斷面的彎矩(N•mm);WB—B-B斷面的抗彎斷面系數(shù)(mm3)。
MB按下式計算:
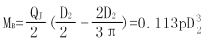
WB按下式計算:

式中:JB—B-B斷面的慣性矩(mm4)。


式中

2.5.3、蝶板的最大直徑
為了防止蝶板在開啟時,不碰撞連接的法蘭管道內壁,設計時應根據(jù)合同要求,按下列公式,來確定蝶板尺寸,如圖5。
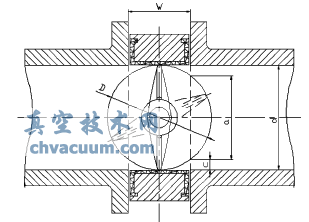
a—蝶板弦長 c—徑向間隙 d—管道內徑 D—蝶板最大直徑 W—最小安裝結構長度
圖5 中線式蝶閥的尺寸位置
首先用下列方程計算蝶板的弦長:
a=d-2c
然后將a值代入方程式確定蝶板的最大直徑:
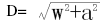
式中:a—通過閥體安裝面與平面的交線確定的開啟位置的蝶板弦長,(如圖5)單位為毫米。C—當?shù)搴烷y門通道處于同軸位置時,蝶板與連接法蘭端面內徑間隙,(如圖5),單位為毫米。一般徑向間隙:DN50-DN150間隙為1。5毫米,DN200-DN500間隙為3毫米;DN600-DN1200間隙為6.4毫米。D—連接管道或法蘭的內徑,單位為毫米;D—蝶板最大直徑,單位為毫米;W—閥門的最小安裝結構長度,單位為毫米。
2.5.4、閥軸直徑的確定
閥軸的最小直徑見表4。最小直徑是根據(jù)蝶閥閥軸計算結果,參照AWWAC504相關規(guī)定進行修改確定的,經(jīng)過多年的使用,證明是可靠的。
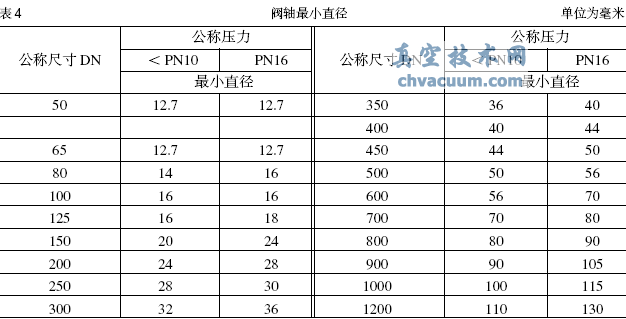
2.5.5、蝶板與閥軸的連接
(1)蝶板與閥軸,常規(guī)閥門的設計是分開的,如圖6(a),通常采用鍵或花鍵連接,也有采用方形軸或銷連接。如果氟塑料襯里蝶閥采用這樣的連接方式,不僅襯氟工藝性不好,使用效果上也有問題。蝶板與閥軸連接的部位在反復交變受力過程中,容易損壞襯里層,導致鋼制骨架受到腐蝕性介質的腐蝕而失效,從而縮短閥門使用壽命。所以氟塑料襯里蝶閥的閥軸與蝶板通常設計成連體形,如圖6(b),實踐證明,這樣的設計使用效果較好。
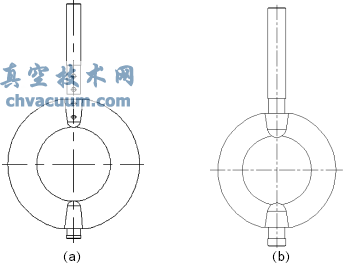
圖6 氟塑料襯里蝶閥的閥軸與蝶板設計
(2)蝶板與閥軸的連接應牢固可靠,在有壓力的工況條件下應保證閥軸的任何部分不致從閥門內射出。蝶板與閥軸的連接應在氟塑料
襯里前完成。連接的方法多樣。蝶板與閥軸可以整體鑄造,也可將蝶板與閥軸焊接連接或鉚接。前提是牢固可靠,不松動。
(3)為了保證蝶板上的氟塑料層與基體緊密結合,可采用φ6毫米的小麻花鉆頭均勻地鉆些穿孔,孔的數(shù)量根據(jù)蝶板的面積大小確定。如圖7。
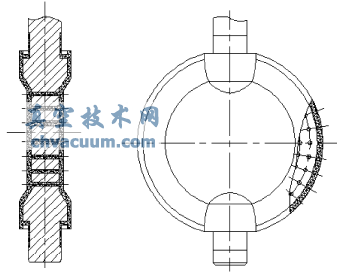
圖7 蝶板上的小麻花鉆孔
(4)由于氟塑料的絕緣性特別好。蝶板與閥座之間在開啟與關閉時,摩擦所產生的靜電難以釋放。因此,蝶板與閥軸之間以及與閥體之間應設計成靜電連通結構,從而通過管道接地,消除靜電積累。
2.6、流阻與流量系數(shù)
流阻與流量系數(shù)的大小是衡量氟塑料襯里蝶閥質量優(yōu)劣的一項重要指標。我國JB/T53171標準將ISO/TC153/SCIGT8-37的流阻與流量系數(shù)列入其中(見表5)作為考核閥門性能的一項指標,供用戶選擇。氟塑料襯里閥門應將流阻與流量系數(shù)值列入閥門性能指標中,以檢驗所設計制造的產品是否達到標準要求。
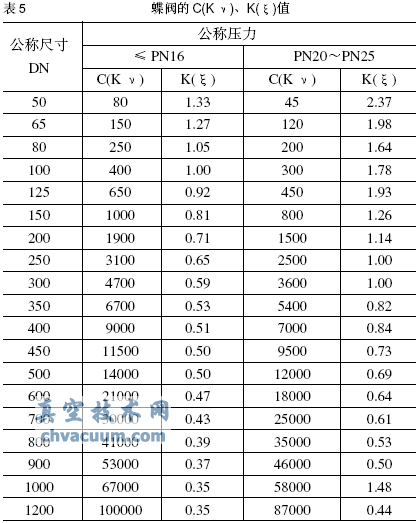
2.7、閥門扭矩
啟閉扭矩小是氟塑料襯里蝶閥的一大特點。在國外很多產品的說明書上,都將閥門扭矩作為一項技術參數(shù)列入其中。在我國一些知名品牌的閥門樣本上,也將本公司設計制造的閥門啟閉扭矩列入,方便用戶選用。一些開啟靈活,扭矩小的閥門深受用戶歡迎。
蝶閥扭矩可由下列公式近似計算得出:
MD=MM+MC+MT
式中:MD—蝶閥閥軸扭矩,N•Mm;MM—密封面間摩擦力矩,N•mm

qM—密封面必須比壓,MPa;R—蝶板半徑,mm;bM—密封面接觸寬度,mm;fM—密封面間摩擦系數(shù);h—閥軸與蝶板中心的偏心距,(中線式為0),mm;Mc—閥軸軸承摩擦力矩,N•mm
MC=QCfCdF/2
QC—作用在閥軸軸承上的載荷,N•mm;fC—軸承摩擦系數(shù);dF—閥軸直徑,mm;MT—密封填料的摩擦力矩,N•mm
MT=QT•dF/2
MT—閥軸與填料的摩擦力,N;QT=φdFbT;φ—系數(shù);bT—填料深度,mm;p—計算壓力,MPa
蝶閥的扭矩也可采用扭矩試驗機直接測得。將計算值與測量值比較,驗證產品的性能。
值得說明的是,受加工工藝及材質選用等因素的影響,閥軸實際扭矩與計算扭矩公稱尺寸小于DN300時略有差別,公稱尺寸大于等于DN300時扭矩差別較大。表6所列數(shù)據(jù)系國內外生產商的典型個案,只限于DN65~DN300之內,供設計制造時參考。
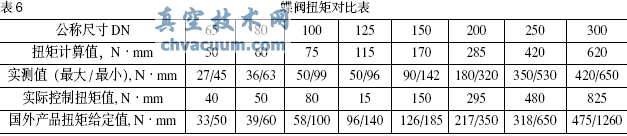
3、殼體材料與襯里材料
金屬材料按表7選用,襯里材料按表8選用。
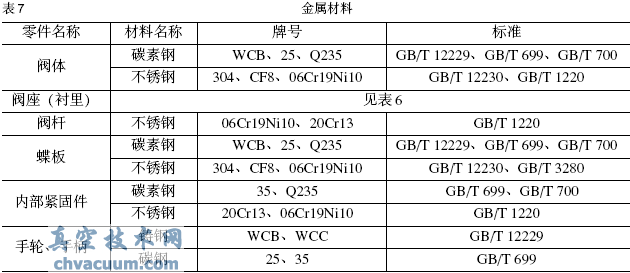
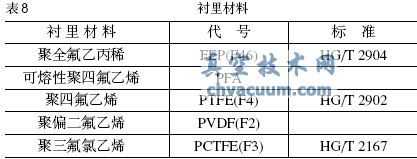
4、氟塑料襯里層的質量要求
氟塑料襯里閥門的表面應當光滑平整、無氣孔、裂紋、夾渣等缺陷。法蘭的翻邊處及其他轉角處應色澤均勻,無泛白現(xiàn)象。并符合GB/T23711.1-2009和GB/T23711.6-2009的規(guī)定。氟塑料是高分子材料,有數(shù)據(jù)表明,氟塑料密度越大滲透系數(shù)越小,它們之間有線性關系。氟塑料襯里層的密度應≥2.16g/cm3,且不允許有雜質存在。
氟塑料的防腐蝕性能,必須達到標準的規(guī)定。如不能確定氟塑料的防腐蝕性能,必須按GB/T1763的規(guī)定做試驗確認。特別是在更換新牌號氟塑料時要作試驗。用于食品、醫(yī)藥、衛(wèi)生級閥門的襯里材料,還應無毒、無菌、無雜質清潔衛(wèi)生的材料,符合GB/T17219的規(guī)定。
氟塑料與基體的結合強度,是衡量襯里質量好壞的標準之一。氟塑料襯里層應與基體貼合,法蘭面的襯里層應襯滿密封面,并且有扣緊基體的設計結構,襯里層在負壓0.08MPa條件下,氟塑料襯里層不出現(xiàn)凸起現(xiàn)象。
5、制造工藝
5.1、氟塑料襯里前的表面處理
閥門襯里前,應將受襯面毛刺、油污清除干凈、修磨平整,盡可能使受襯面達到GB8923中規(guī)定的St2級,還可以采用機械加工的方法,將受襯面加工出T形槽和螺紋溝槽,增加襯里層與基體的結合強度,防止襯里層脫殼。將襯里面內部轉角處的棱角銳邊倒鈍,內圓角R>2mm,外圓角R>3mm,減少應力,防止襯里層被銳角刺破。應盡量滿足襯里工藝的要求。
5.2、模壓成型
將需要模壓的蝶閥零件放入模具中,送入加熱爐內加溫,加溫到一定溫度,如將氟塑料加熱到290℃~370℃使其熔融,在7~12MPa壓力下,使熔體充滿模具、壓實,冷至150℃脫模即待到制品。見工藝流程圖。

圖8 模壓成型工藝流程圖
5.3、模壓工藝
模壓(如圖8)是氟塑料襯里跌蝶閥最常用的一種方法,適合于多品種小批量的生產方式。它是將一定量的氟塑料(粉狀、粒狀、纖維狀、片狀和碎屑狀等)放入成型的模腔中,然后閉合,放在加熱爐內加熱到一定溫度,取出來,放在壓力機中在壓力作用下熔融流動,緩慢充滿整個型腔而取得型腔所賦予的形狀。隨著在模具內塑化、混合和分散,熔體逐漸失去流動性變成不熔的體型結構而成為固體,并不斷用冷水冷卻,冷卻到一定溫度打開模具,而成為成品,從而完成模壓過程。氟塑料襯里層的質量主要取決于氟塑料原料質量、襯里模壓工藝和模具的設計。
氟塑料襯里閥門成型質量包括襯塑層的內在質量和外在質量。內在質量包括襯塑層的物理和化學性質及其均勻性;它不僅要求氟塑料具有相應的物理和化學性能。在模壓過程中,還要注意塑化的溫度和壓力,正確掌握模壓工藝。外在質量包括襯塑層的尺寸、外觀和色澤等。襯塑層的外表面質量主要取決于模具的設計和氟塑料在模具內的塑化、混合和分散的能力。塑化效果與模具結構以及工藝配方、原料質量和加工工藝條件的控制有直接的關系。
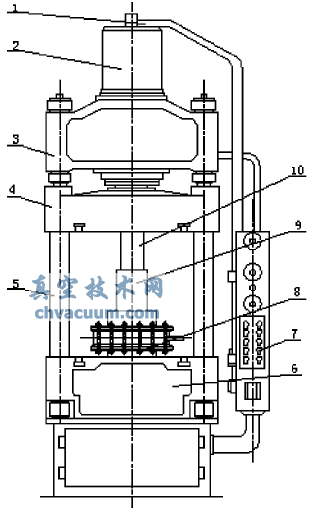
1.主柱 2.活動橫梁 3.上橫梁 4.油缸 5.油管 6.壓頭 7.模具與料筒 8.閥體 9.操縱箱 10.下橫梁
圖9 油壓機與閥體模壓示意圖
塑料塑化成型對溫度和壓力的要求非常嚴格,掌握氟塑料的塑化時間非常重要。塑化時間太短,氟塑料未成型就已分解交聯(lián);若塑化時間太長,則生產效率低,需要很長時間才能固化脫模,生產周期長。在生產中,控制塑化時間的關鍵因素就是溫度和壓力。若不能控制好塑化溫度和壓力,則很可能產生諸如襯里層表面硬度低、表面光亮度不足;襯塑尺寸控制困難;熔接痕難以消除;襯塑層沿氟塑料流動方向有“魚鱗”樣凸凹不平的有規(guī)則的波紋,或表面箭頭狀波紋等問題。值得一提的是在加壓過程中放氣次數(shù)、放氣時間、間隔時間都對襯塑層的外觀質量有直接影響,在生產中應嚴格控制,并做好生產記錄。工藝人員可以在生產前對氟塑料擬訂其塑化曲線,掌握其塑化時間,然后在實踐中根據(jù)實際情況進行工藝調整。因每種產品的公稱尺寸、公稱壓力不同,氟塑料配方、原材料質量、要求各異,其溫度、壓力,放氣等工藝控制也不盡相同,根據(jù)具體情況決定,從而制訂出符合本企業(yè)的模壓工藝。
6、結語
氟塑料襯里蝶閥在設計制造工藝上與常規(guī)蝶閥相比,有相同的地方,也有不同的地方,本文力求全面介紹氟塑料襯里蝶閥的設計要點、制造方法、工藝特點,幫助讀者了解襯氟蝶閥。
氟塑料襯里蝶閥的出現(xiàn),是科學技術進步的產物,是對常規(guī)蝶閥產品的創(chuàng)新,不僅節(jié)約了大量的稀有金屬,合理的利用了資源,而且還節(jié)能、環(huán)保。滿足了石油化工工業(yè)對特殊閥門的需求,經(jīng)濟效益和社會效益特別顯著。值得推廣應用。